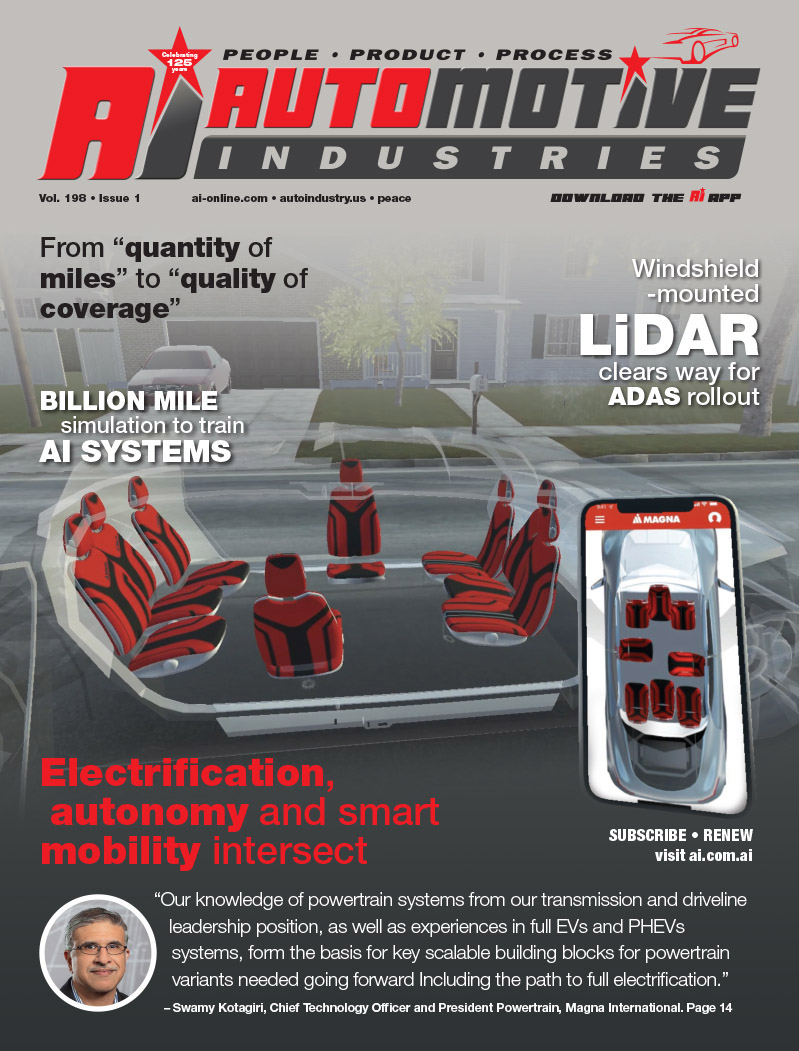
The German Gesellschaft fuer Emissionstechnologie GmbH or Emitec, is a global leader in the metal substrate market for vehicle exhaust gas catalysts and diesel particulate filters. The company also supplies optimum serial-production ready components and systems for emission reduction methods. Currently, the company is poised for greater growth as the January 1st 2010 EU deadline to cut nitrogen dioxide emissions to 40 µg/m3 has kicked in. For this challenge, Emitec has showcased its turbulent METALIT® honeycomb as the solution.
Emitec’s turbulent catalysts and particulate filters are efficient and require small space, and it results in low pressure loss and low weight. As a result, they are ideally suited to meet future, substantially tightened emission limits. “Thanks to their turbulence-generating profiles, EMITEC products offer specific advantages, such as improved mass transfer, lower thermal mass and improved flow distribution, making it possible to realize ultra-compact and highly efficient close- coupled systems without difficulty,” says the company.
For direct-injection diesel and petrol engines Emitec and its associates developed SCRi® a very compact exhaust gas treatment system, to cut emissions well below the even stricter particulate matter limits and the new, tighter nitrogen oxide limits. SCRi® systems (= SCR with integrated particulate reduction) include a compact PM soot filter (PM = particulate matter) with an integrated oxidation catalyst, followed directly by an SCR NOx reduction stage that consists of an SCR catalyst with turbulent Metalit® LS-/PE-structures. The application of SCR technology and selective catalytic reduction cuts NOx levels by over 90 per cent and particulate emissions by over 80 per cent. These figures can be substantially increased through the use of larger components. Its modular concept also makes SCRi® suitable for retrofitting.
For all kinds of diesel and petrol engines, Emitec’s pre-turbocharger catalysts provide higher temperature levels than other catalysts and improve the HC/CO light-off behavior of the overall system. This is because the company’s pre-turbocharger catalysts use the turbulent Emitec catalysts. Highly efficient exhaust gas treatment means that even extremely small catalyst volumes, between 50 and 200 cm3, can make a significant contribution. Despite their small size they are able to reduce carbon monoxide emissions by up to 50 per cent. Also, cost savings are considerable as these catalysts cut the amount of precious metals in the downstream oxidation catalyst.
For diesel engines and future petrol engines, the PM-METALIT® soot filter offers a good option. In contrast to wall-flow filters, a PM-METALIT® filters particulates using partial-flow deep-bed technology. Unlike conventional filters, it cannot block, if properly applied, and so ensures efficient and unrestricted engine operation under any operating conditions. Since the system requires no diesel post-injection for active regeneration, vehicles with a PM-METALIT® soot separator use less fuel and consequently produce less CO2. This results in low pressure loss when compared to conventional filters saves even more fuel/CO2.
A decade ago, Emitec first used its electrically heated catalysts in the 12-cylinder engines of the Alpina and BMW 7 series. The 1 to 3-kW heated metal catalysts rapidly increase the operating temperature by up to 100°C in passenger cars (30°C in trucks), resulting in extremely fast light-off behaviour in the vehicle after a cold/new start.
“A new, fast heating and economical catalyst, specifically designed for diesel engines, which is currently undergoing series trials, will be presented at the IAA. The injection of an AdBlue urea solution onto the hot EHC further improves evaporation in an SCR system. The fact that the exhaust after-treatment system becomes effective at a much
earlier stage substantially improves emission test results so that the size of the components or the precious metal content can be reduced. Modern energy management (using brake energy recuperation) enables the EHC to operate potentially even more fuel-efficiently than comparable engine heating measures,” said Emitec in an earlier press release.
Automotive Industries spoke to Claus Bruestle, president of North American operations at Emitec Inc.
AI: What are the latest developments in emission control solutions?
Driven by an ever increasing demand for lower emissions regarding NOx we see the Selective Catalytyc Reaction systems, SCR, for Diesel engines as one of the most challenging developments in Europe and the US.
NOx levels of 0.2 g/hp/h as required by the EPA regulations for 2010 force the engine and aftertreatment industry into the adoption of complex aqueous urea storage and injection systems, their electronic controls and reliable NOx conversion within the catalytic converters. At the same time so called “high EGR systems”, EGR stands for exhaust gas recirculation, are complimentarily or in some cases as sole solution developed in order to maximize fuel economy and minimize engine out emissions.
On the engine side huge efforts are being undertaken to increase injection pressures to 3000 bar and above to lower those raw emissions, particulates mainly, to offer best starting conditions for the NOx and PM trade off and fuel economy.
Having the particulate mass under control , the particulate count regulation in Europe, which is expected to take place in 2013 and is most probably also in discussion in the US, will create even new challenges towards the aftertreatment technologies. Cordierite particulate filters will have to be redesigned towards lower levels of porosity which will make their application on diesels a challenge due to high backpressure for the engines. And even increasing backpressures during engine operation will create new obstacles for the engine combustion calibration especially under transient conditions.
Besides all cleaning efforts the CO2 reduction will be a key concern as some of the emission reduction technologies are counter productive for fuel economy.
AI: What are some of Emitec’s catalytic solutions for OEM gasoline and diesel applications?
Our perforated foil technology, PE, is extremely suitable for gasoline engines requiring lowest possible thermal mass of the catalytic converter, again driven by cold start requirements. This design allows cross flow inside the catalytic converter from one channel to the other. During unfavourable inflow conditions, mostly forced by inlet cone packaging requirements can be compensated leading to an equal flow distribution within the converter and reduces backpressure while enhancing efficiency and PGM utilization of the device. These advantages can be used to futher minimize the needed catalytic converter volume which results in lower weight and cost.
With the to be expected spread of down sized direct injected turbocharged gasoline engines and also their stratified derivatives the diesel and gasoline exhaust gas aftertreatment requirements will become very similar. In particular the particulate emissions of these engines will require attention, as the particulate size distribution is shifted towards very small, so called Nano particulates. Especially for these types of particulates the Emitec partial flow PM-Metalit filtration is highly effective due to diffusion and adhesion effects on our fine fleece designs, without increasing back pressure to the engine.
Still the exhaust temperatures at full load will be considerably higher on the gasoline side which drives us and our coating companies collegues to the development of even higher heat resistant materials and designs than used today.
In addition we are able to optimize catalytic converter applications in a superior way as our designs allow high flexibility in cross section shapes, triangular, theta, oval and even egg shapes to utilize given package space in modern vehicles most effectively.
For diesel engines, heavy duty on road and off road, as well as light duty vehicles, Emitec developed their SCRi system. This solution, which comprises a highly efficient metal diesel oxidation catalyst, DOC, with longitudional shovel structures in the flow paths, turbulent LS technology, a PM-Metalit, our deep bed partial flow particulate reduction device and a SCR substrate based on our turbulent foil technology offers within the smallest package space highly efficient SCR functionality.
Emitec develops also counter flow UREA injection towards a zone coated metal DOC in order to avoid any additional mixing devices for Ammonia production. Ammonia and residual UREA mix is then routed into our coated PM-Metalit which provides three functions within minimal space: mixing of UREA with exhaust, hydrolysis to create Ammonia and simultaneously particulate reduction. The optimized Ammonia preparation and mixing can be used to minimize the size and weight of the downstream SCR catalyst which in our case is constructed with LS turbulent foil technology which enhances mass transfer and can further reduce the size of the SCR catalytic converter.
For the Diesel oxidation catalyst we are successful with our LS foil technology, which allows to downsize the DOC by about 20% to 30% compared to a straight channel device. Corrugated shovels in the foils create local turbulence conditions enhancing mass transfer greatly.
This technology helps the OEM to save cost of the aftertreatment system, as the precious metal use is a linear function of substrate size at a given specific PGM loading.
Current and future cold start and heat up requirements of diesel engines can be well supported with Emitec’s electrically heated catalytic converter, which is a unique design feasible with the basic metal concept of our products. The device was developed originally for gasoline engines as their main challenge is during cold start and warm up regarding HC and CO emissions.
Pre turbo catalyst designs for diesel engines, which are under development, are another highly effective feature to reduce warm up emissions and create the potential to reduce cost of the overall emissions reduction system. A small catalyst volume before the turbine of the turbocharger can reduce the required total volume of the catalytic converter system, pre and post turbine, such that a cost reduction by saving substrates size and precious metal is achieved.
AI: What is Emitec’s vision of the future of optimized emission control?
The reduction of diesel engine out emissions will be further enhanced by high compressor pressure ratios with multi stage turbocharger systems, further increased injection pressures and spray control and timing and refined accurate EGR control. Similar effort will take place on the gasoline side, diesel and gasoline will become more and more alike.
The electrification of the automobile and heavy duty truck and machinery is on a level today unthinkable 20 years ago.
Emitec’s electrically heated catalytic converter can be intelligently incorporated into this infrastructure providing also CO2 reduction potentials. Heating the catalyst electrically during cold start and warm up conditions is a more energy efficient path compared to todays warm up strategies by engine calibration and combustion measures, which trim the engine towards higher exhaust gas temperatures for exothermic reactions in the exhaust system upstream of the catalystic converter for catalyst heating functionality resulting in higher fuel consumption and CO2 emissions.
The trends in engine technologies offer the aftertreatment industry widened opportunities for communization in technologies and even component design, which will help to control cost to the OEM and finally to the end consumer.
Optimized system solutions, which lead to lowest cost and complexity, are accomplished by a systems approach. This led Emitec towards a strategy to offer the development of complete SCR systems including every component needed to our OEMs customers. This strategy is supported by considerable investments in our engineering and test infrastructures.
Maintaining design flexibility to accommodate application’s special needs without compromising base technology and manufacturing capabilities is certainly one of Emitec’s basic strengths and helps to minimize cost of concept and design .
AI: Tell us a little about some of the solutions you are working on in conjunction with OEMs.
This is touchy as we are in confidential agreements with our OEM customers. Be assured that all of what is stated above is real and is happening.
But let me touch at least on one of our most challenging, and also rather new engine heavy duty exhaust aftertreatment fields, locomotives and power generation.
For these applications mechanical robustness, reliability and long term durability is a key factor. 20.000 hours of undisturbed operation on a locomotive engine is simply standard. For these engines metal substrates for DOC, particulate reduction and SCR functionality is highly attractive due to the robustness and low back pressure properties of our proprietary designs. Also our washcoat company partners do see these new challenges, however being well positioned to apply their DOC and SCR coatings very successfully to our metal substrates and their specially oxidized surfaces.
Another benefit of the mechanical robustness of Emitec’s metal substrates is the opportunity to install the complete aftertreatment on these engines before the turbine of the turbocharger or turbochargers without running the risk of damaging the turbine wheel with lost particles or larger pieces from the aftertreatment system.
This new way of aftertreatment placing reduces the backpressure to the engine considerably which results in better CO2 emissions and torque behavior. On top of this the emissions reduction systems starts to work earlier due to the higher exhaust gas temperature before the turbine.
Most remakbly, due to the higher pressure and temperature level at which the aftertreatment system is running, a size reduction opportunity of the aftertreatment components of up to 50% is offered.
An also highly interesting new development is our thermal energy generator, TEG, which converts exhaust heat into electrical energy. These systems, which are under co-development between BMW and Emitec, allow to further improve fuel economy and reduce CO2 emissions, as waste energy in the exhaust gas is reduced.
AI: What are some of the challenges facing Emitec in new vehicle technologies such as hybrid technologies?
Hybrids must meet like any other vehicle the emissions regulations.
Mild hybrids are very conventional regarding the aftertreatment system, Fast light up after cold start is essential.
As electric energy is generated during brake energy recovery new approaches for warm up strategies with an electrically heated catalyst are possible. Abandoning the catalyst warm up strategies on gasoline engines for cold start, reducing the thermal efficiency of the engine with spark retard and load increase for the sake of adding electric energy instead, has a potential of CO2 reduction of several percentage points as our tests demonstrated.
On full hybrids the range extender engine is a challenge as it must run at power instantaneously. Lowest thermal mass with our PE foil technology and additional electrical catalyst heating will offer viable solutions for immediate catalytic converter function.
AI: Tell us about the new catalyst designed specifically for diesel engines.
The required space for emissions reduction systems became a huge challenge for the OEM and will certainly become even under higher focus in the future. The path going forward is to increase catalytic converter effectivity and efficiency in order to be able to minimize their size and allow closed coupled systems, which are more effective during engine warm up conditions and during low exhaust gas temperatures conditions of highly efficient diesel and stratified gasoline engines.
The path forward is to use turbulent foil designs.
LS for longitudinal structures, offer the most efficient and cost effective solutions for the diesel oxidation catalyst. In addition we developed specific foil materials to accommodate the diesel temperature requirements which further optimizes durability and cost to the OEM.
Combining this technology with Emitec’s integrated SCR system, SCRi, which offers a unique integrated and package space optimized SCR system’s approach, will deliver highest design flexibility, smallest package requirements, lowest weight and at the end the most reliable and cost effective solution to the OEM and the end user of cleaned vehicles and machinery.
More Stories
Huntsman Polyurethanes introduces a new range of polyurethane-based products developed for battery enclosures, battery cell potting and underfloor protection
Lakshmi Prasad Bhatta on the quest for zero road deaths
NXP accelerates the development of software defined vehicles with new family of Ethernet switches