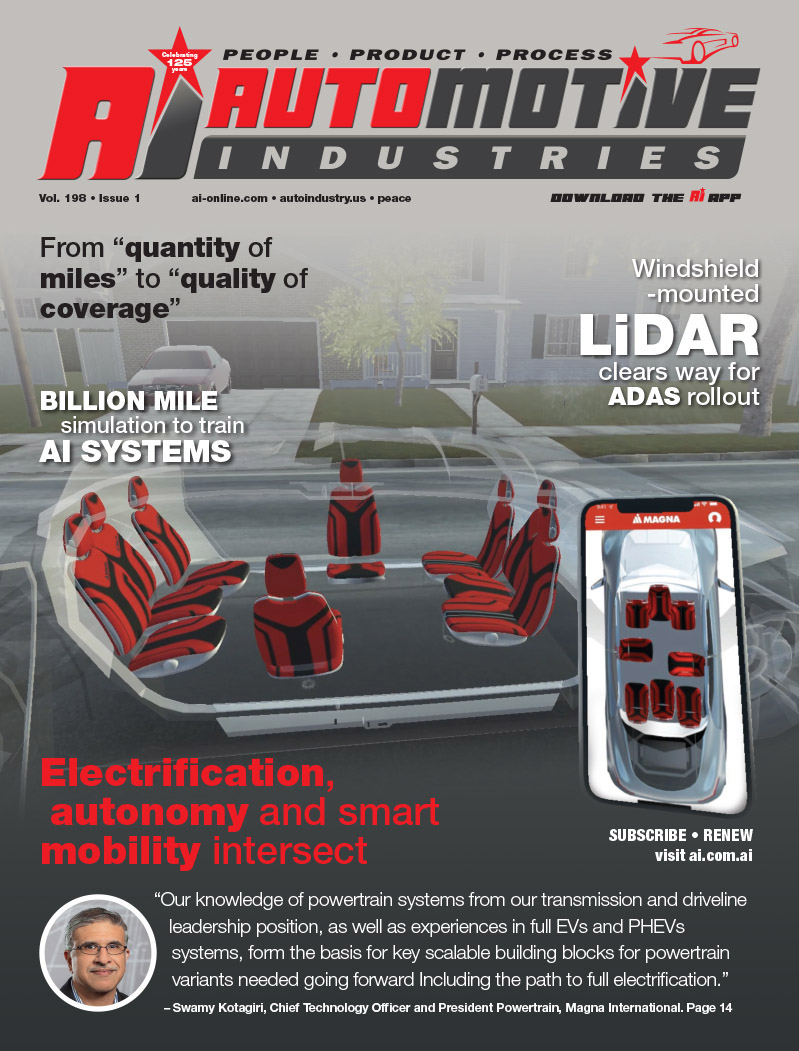
Apriso, a leading provider of manufacturing software solutions for sustained operations excellence, announced Shanghai General Motors Co., Ltd. (SGM) has implemented Apriso’s FlexNet® for Quality Containment, as part of initiatives to improve tracking of materials across production, reduce the cost of quality and increase manufacturing efficiency.
SGM faced several challenges in maintaining its high quality standards. Prior to Apriso, limited visibility and control over third party logistics provider shipments led to possible production delays when out-of-spec parts were delivered. Because of this, it was difficult to quickly and efficiently identify and isolate any work-in-process impacted by the out-of-spec part or process. If a production line change was needed at the machine level, the time and resources to complete was cumbersome, with 100+ machines involved in a single product line.
With Apriso’s FlexNet for Quality Containment, SGM has seamlessly integrated quality containment across manufacturing operations, helping to provide global visibility and control over production and logistics processes to complement other SGM Powertrain systems while integrating with their SAP ERP system. The quality containment system accurately identifies and contains product in the event of a quality problem – from production through Work-in-Process to minimize associated costs and prevent out-of-spec products from being sent to customers. Order information is retrieved from SAP and then automatically updated in SAP as materials, product count or order status changes; resulting in avoidance of manual data entry errors and the related delays.
“FlexNet Containment Manager easily allows us to identify and quarantine an engine or parts by multiple criterion, such as operation time, operator, work center, child or parent parts,” explained SGM Project Manager Han Pengjun at Shanghai General Motors Co. “Out-of-spec work-in-process can now be held and not shipped to our customers, helping to improve customer satisfaction.”
Apriso’s FlexNet Machine Integrator has also been leveraged to centrally manage SGM’s production machines through a web-based user interface that is much more efficient, accurate and faster than the prior manual process performed at the machine layer. Adjustments can be performed from remote locations, helping to improve SGM’s manufacturing responsiveness and agility.
“Apriso has helped Shanghai General Motors achieve significant cost reductions by transforming their manufacturing operations into a collaborative, responsive set of processes and interlocking systems,” explained Jim Henderson, president and CEO of Apriso. “When facing considerable demand fluctuation and unknown supplier quality for work in process, manufacturers need to respond by building in considerable flexibility in their production systems to contain potential quality issues and ensure customers receive the highest level of service and finished goods.”
About Apriso
Apriso Corporation is a software company dedicated to providing competitive advantage for its customers. It does so by enabling organizations to adapt quickly and easily to market changes and unexpected events. Apriso’s FlexNet platform provides visibility, adaptability and real-time control of manufacturing operations across the enterprise and supply chain network. This is accomplished by integrating planning, execution and control, increasing operational efficiency and eliminating errors in the production process. Apriso serves more than 175 customers in 41 countries across the Americas, Europe and Asia. Its customers include General Motors, Lear, Honeywell, L’Oréal, Trixell, Lockheed Martin, Becton Dickinson, Saint-Gobain, Novelis and Essilor, among others. For more information, please go to www.apriso.com.
Apriso and FlexNet are registered trademarks of Apriso Corporation. All other trademarks and registered trademarks are the property of their respective owners.
About Shanghai General Motors
Established on June 12, 1997, Shanghai General Motors (SGM) is a 50-50 joint venture partnership between General Motors and the Shanghai Automotive Industry Corporation (Group), or SAIC. To date, SGM has three major manufacturing bases, Jinqiao in Pudong, Dongyue in Yantai, and Norsom Motors in Shenyang, as well as four vehicle production plants, and two powertrain plants. The annual production capacity of SGM is expected to be more than 600,000 units, 870,000 engines and 380,000 automatic transmissions. SGM has ranked first in the passenger car market in 2005, 2006 and 2007 in terms of sales volume. SGM is also the only automaker that received the title of “China’s Most Respected Enterprise” for seven consecutive years, and is an important player in the automotive industry of China.
With its customer-oriented and market-driven philosophy, Shanghai GM satisfies an ever-growing market demand by offering rich product lines and superior services. Today, Shanghai GM is a multi-brand company with 22 product lines including world-renowned brands Buick, Cadillac, Chevrolet and Saab, and boasting over 80 models. Covering the broad segment range of luxury, entry-level sedans, and MPV & SUV, all SGM vehicles represent the most advanced products in their segments.
Shanghai GM initiated the comprehensive “Drive to Green” program in January 2008. SGM has made “developing green products, insisting on green manufacturing, undertaking green responsibility” its long term strategy and grand mission. In terms of technology innovation, Shanghai GM will provide Chinese consumers with green vehicles featuring better performance, less fuel consumption, and lower emissions. At the same time, SGM plays a leading role in the business chain, building a green industry ecosystem with partners both upstream and downstream, ensuring the company, industry and environment to develop in a harmonious and sustainable manner.
More Stories
New version of Microwave Switch Design Tool from Pickering Interfaces on show at European Microwave Week 2024
Fusion Processing Announces Readiness for Commercialisation of Automated Trucks and Buses
Rita Case Presented with Lifetime Achievement Award from National Association of Minority Automobile Dealers