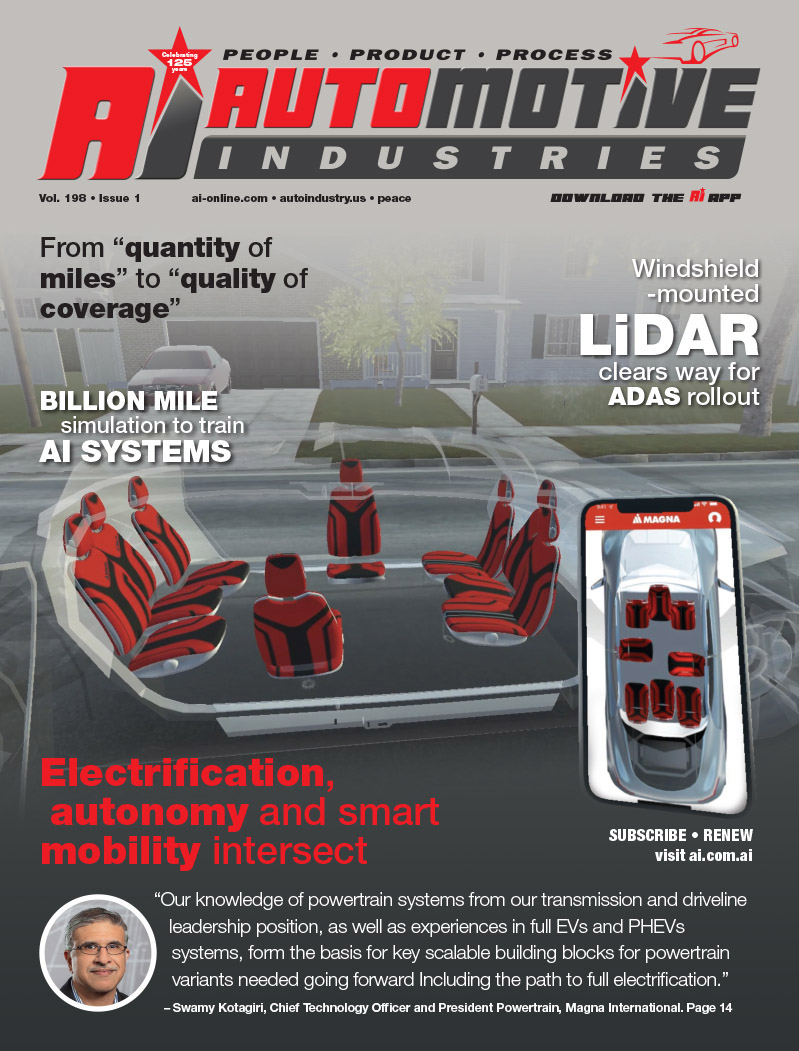
Quality is a key factor when it comes to engineering and manufacturing components, structures and complete seats for commercial vehicles, and Keiper has been doing it for 88 years. Automotive Industries (AI) spoke to Joachim Thamm, Vice President Central Quality at Keiper, and asked him what he company is doing to raise the bar on quality.
Thamm: In order to strengthen the focus on quality, Keiper set up a Central Quality Department in 2006. Our customer service teams visit Keiper customers on a regular basis to ensure they are totally satisfied. For products that are engineered in Germany, but manufactured in other countries, we manage the coordination and implementation of advanced quality planning in the early project phases. In this respect, we get the production facilities involved as fast as possible. In order to discuss special issues and work together to develop new methods and standards, our international quality experts meet several times a year and hold biweekly global telephone conferences.
AI: Who takes responsibility for quality?
Thamm: Our plant managers are ultimately responsible for the quality of the products supplied. Their job is to implement all of the required measures and activities to ensure maximum quality. For the analysis of complex problems, support is provided by a group of Six Sigma experts, specialized in statistical methods. This ensures that the primary causes are specifically identified based on process data. In order to evaluate the level of success on a monthly basis, we have introduced internationally standardized quality reports with defined KPIs – key performance indicators. Along with the key data, these reports include the TOP quality challenges for the previous month. When there are deviations from the set targets, our plant managers are required to provide a detailed analysis of the cause – along with a corresponding action plan. Keiper practices a philosophy of shared learning. Best practice identification and best practice sharing ensure a dynamic exchange of knowledge within the company on an international level.
AI: Are all Keiper sites certified?
Thamm: Our quality management system is standardized across all Keiper production sites in Europe and Asia as well as in North and South America. All Keiper plants are certified according to ISO/TS 16949 quality standards. They also comply with ISO 14001 environmental management specifications.
AI: What are the results of your quality policy?
Thamm: Quality is something that has become ingrained in the minds of all Keiper employees. Each individual takes quality seriously and personally strives to make continuous improvements. This isn’t just an empty claim – our key performance indicators speak for themselves. For example, our ppm rate was in the mid triple-digit range in 2006. Today, the annual average for 2008 is in the very low double-digit range – and this number is continuing to sink. In the month of September, Keiper set a new record with only two defective parts per million. The number of customer complaints has also been reduced by more than half compared to 2006.
AI: What are your goals for the future?
Thamm: Our goal is zero defects. And this starts with the first part supplied. We rely on robust products and manufacturing processes that keep our defect rate in the single-digit range – i.e. consistently less than 10 parts per million. As part of our holistic quality policy, we expect our suppliers to achieve the same level. After all, it takes zero-defect parts to build zero-defect products.
AI: Does Keiper quality policy cover the services as well?
Thamm: When it comes to our customers, we focus on quality in services as well as in our teamwork. At the same time, we regard our suppliers as key partners who become involved in the early phases of our engineering processes – with increasing intensity – and receive active support if necessary. This is the only way they can significantly help us meet our quality standards. We have already accomplished a lot in this area.
AI: What prompted the creation of a corporate quality department?
Thamm: We were no longer satisfied with just being “good”. Our aim was to concentrate the available strength and potential at Keiper to be the best. This requires uniform, company-wide methods and standards. To ensure these standards apply on a long-term basis, the international lines of responsibility must all come together in one place.
The implementation of various standards and processes must always be an interdisciplinary task. Instead of cooperating only with the specialists in product development, industrial engineering, purchasing or operations, the Central Quality team works with all Keiper divisions. The main focus is clearly on the product development process based on the principle: quality first has to be developed before it can be produced. Any attempt to ensure quality through a series of costly, after-the-fact inspections is not only extremely expensive, it is simply not effective on a long-term basis.
AI: What are the main processes that you employ in order to ensure customer satisfaction?
Thamm: Customer satisfaction is a mission that applies without exception for all production sites, departments and employees across the company. The main target is to ensure that quality problems never even appear at the customer’s end. And if they do, our job is to ensure a quick and professional response. With this in mind, we created the Requirement 24 process to handle complaints. This means that customers receive a definite response within 24 minutes and are fully protected against defective parts within 24 hours. Internally, we are required to take action company-wide within 24 days to ensure the problem does not reoccur.
The regularly-scheduled quality assurance meetings held with senior managers play an equally important role. This is where the plants report on the external and internal quality issues experienced over the preceding quarter. The aim is to scrutinize the effectiveness of our system and identify potential weak points.
In order to set the right priorities for quality and remedy system weaknesses in their areas of responsibility, managers must be kept up-to-date with the right information. Keiper operations are based on the EFQM (European Foundation for Quality Management) model. This holistic approach is used to clearly identify the company’s strengths as well as areas for improvement and take appropriate action. Before something can be improved and subsequently evaluated for its effectiveness, it has to be measurable. The objectives are derived from the market benchmark. Our objective is to serve as the industry’s benchmark. This is our way of guaranteeing our customers a level of quality that is not just satisfactory, but unconditional.
AI: What measures for continuous improvement do you have in place?
Thamm: One of the things we are doing is to focus more on the product development process to ensure quality is integrated into the concept based on DFSS – Design for Six Sigma – guidelines. We are also standardizing our production methods so that they are more in line with the “Quality System Basics” developed by GM. Our new plant in Skarbimierz, Poland is destined to become a best-practice site within the Keiper network. A series of training workshops and exchange programs will make this knowledge available to all Keiper plants. As part of Requirement 24, we have innovative software in the pipeline that was developed in-house. Along with a further increase in efficiency, this will enable us to more quickly and precisely identify areas of activity for optimizing our products and processes. For us, it is less important to maximize the number of methods and processes. The key success factor lies in implementing a limited number of measures as fast and consistently as possible.
More Stories
ROHM to Showcase Advanced Power Electronics at APEC 2025
ROHM Launches 650V GaN HEMT in a Compact, High-heat Dissipation TO-Leadless Package
ROHM’s New TVS Diodes: Supporting High-Speed CAN FD In-Vehicle Communication Systems for Autonomous Driving