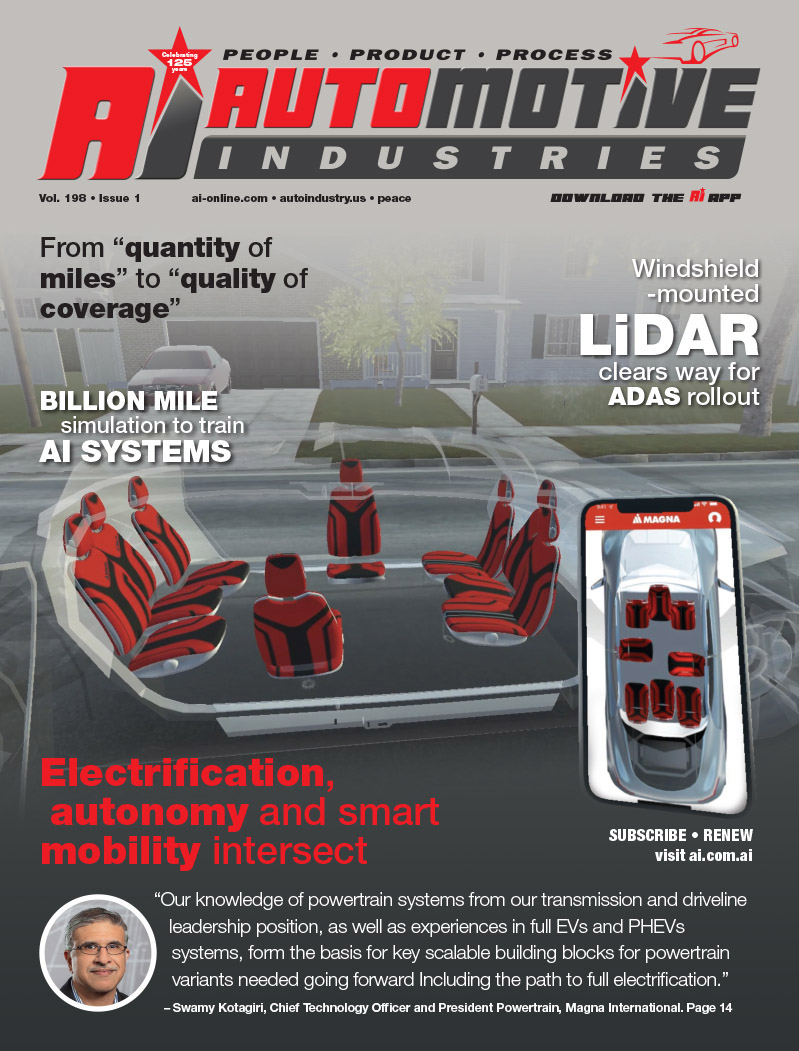
The 2.8 billion Euro Luvata Group, a leading international supplier of metal solutions, services and components, recently restructured its heat transfer automotive division. The division manufactures copper and brass strip for automotive applications such as car radiators, as well as for other industrial markets. Competition from low-cost countries combined with higher prices of copper hit Luvata. The company says it will be slashing production by 10 to 15 per cent this year. And at the same time, will be increasing its focus in its core competence of supporting the automotive industry.
The Luvata Group, is a conglomerate of 35 companies that employs a total of 6,500 employees and has 27 factories and a presence in 13 countries. In its strategy to focus on the global automotive industry, the company opened the largest resistance-welding consumables factory at Suzhou, China late last year with an investment of USD 3 million. Resistance welding caps are used by automotive manufacturers to weld car bodies and panels. The Luvata products – under the brand names of Nitrode, Z-Trode, A-Trode, C-Trode, Cupal, and Nitrode Composite – are used by leading manufacturers in the Asia Pacific region, including Honda, General Motors, Volkswagen, Toyota and Citroen.
The Suzhou facility is Luvata’s third such plant of this type. It incorporates technology that has already been proven in Luvata’s facilities in Delaware, USA and Welwyn Garden City in Britain. Luvata’s advanced welding electrodes are made from special alloys and composite materials and are renowned for their high working quality.
“The new plant is another illustration of our dedication to being a global supplier. Car manufacturing is a global business that remains particularly strong in Asia. Suzhou will enable us to focus on the ongoing, huge demand for welding electrodes in this region. It’s an aggressive industry, often with very short lead times, so we need to be close to where the action is. This plant will make sure that we can stay responsive to our customers,” said Jussi Helavirta, executive vice-president of Luvata’s electrical and industrial division.
According to the company, its 25 micron thin radiator strips, resistance welding electrodes, special wires, connector strips, tub and e-cooling profiles, are found in or used in production of nearly all cars, trucks, buses and off-road vehicles today. The company is a major supplier to the automotive industry and has focused on making quality a priority. Luvata has the ISO 9001/2000 and TS 16949 certification and complies with the environmental regulations IMDS-database, VDA and EU Vehicle End-Of-Life Directive 2000/53 EG.
“Up to 90% of all new features in our cars are based on electronics. Car manufactures use innovations such as GPS navigation, ESP, ABS, Car-phones, on-board computers, emission controls, anti-theft devices, park and cruise distance controls as well as engine and transmission management systems as competitive advantages. Luvata Austria uses Alloys like CuMg, CuFe and CuAg to manufacture high quality plated and bare wires. The key advantage of these alloys is the combination of high electrical conductivity and high tensile strength. Automotive connectors and terminal blocks are an excellent area for the use of these alloys. Both types of connectors are subject to high Amperage stress and the pins must be of high tensile strength for safety reasons,†says a statement on the company website.
Luvata was earlier known as Outokumpu Copper Products, and acquired from Outokumpu OYJ in 2005 by Nordic Capital. The company’s headquarters are located in Britain.
Automotive Industries spoke to Jerker Adeberg, president of the Heat Transfer Automotive division of the Luvata Group.
AI: Please tell us what Luvata’s Heat Transfer Automotive division will look like after the restructuring exercise.
We currently have two factories manufacturing products for our Heat Transfer Automotive division. This will not change following the restructuring. Both of these factories manufacture for global markets, with a combined sales-force supported by R&D teams and technical engineers. These factories work primarily with copper, brass and CupraBraze, bringing products to the heavy duty automotive and engine markets. The restructuring exercise simply aims to streamline our Heat Transfer Automotive operations to ensure our continuing profitability.
AI: How important is the automotive part of your business in the overall scheme of your businesses?
Due to its global growth the Automotive sector is a key priority for Luvata. Our work in the sector does not focus solely on copper and brass – we have to look at other materials like aluminium to be able to fully support the total Automotive sector and utilise our skills, applications and engineering expertise. Our focus is to support our customers’ needs throughout the total sector – this requires us to look beyond copper, brass and CupraBraze.
AI: It looks like Luvata’s Heat Transfer Automotive division is focusing on shifting out of high-cost Europe to low-cost Asia – is this a correct observation? And if so, how easy or tough will it be to keep quality standards high?
This is not the case at all. We want to develop and utilise our techniques for Heat Transfer Automotive in Europe further, rather than move this work to Asia. Our main two production facilities in Sweden and Holland remain central to Luvata’s Heat Transfer Automotive division. We are working to make these more competitive by working on ‘optimisation’ projects – for example, Luvata’s production system. We want to be as competitive as possible across the globe. We have excellent quality standards in Europe and we are confident that our facilities will bring to market products of an excellent quality. Our integrated and vertical casting gives us an advantage when producing thinner gauges.
AI: Apart from Asia, what are the other regions Luvata has identified to expand in?
Europe and the US remain key focus areas for expanding our manufacturing base . This is against a backdrop of continuing to build our global market sales. In terms of future sales, we will continue to view their potential globally and our specific focus will be driven by individual customer needs.
The Heat Transfer Automotive division has many global customers who have production plants in Europe, the Far East, USA and Australia and they want to use same quality products across all their plants worldwide, and for this they need us to supply consistent quality products to all plants.
AI: What are some of the Heat Transfer Automotive division’s strategies in increasing its global client base?
We are running development projects with some truly global players like Denso, Modine, Behr etc. We follow them when they restructure and centralise. For example, if they introduce global purchasing and R&D we can support these customers with our global capabilities. For each individual customer we reshape our business model and approach and can adapt to reflect their requirements.
As for new customers, we have the best understanding of our customers’ customers’ customer! We know what the final end user wants – and what they expect from our products, particularly the added value they can bring. Luvata’s Heat Transfer Automotive division has the reputation for being ‘the supplier of choice’ for many international organisations.
More Stories
Bangkok International Motor Show 2025 – The Talk of Sensuous Automotive
Dry silicon composite by Blue Current is the next generation of battery technology
GlobalLogic Pioneering Software-Defined Vehicles, AI Innovation, and Sustainable Solutions for the Future of Automotive Mobility