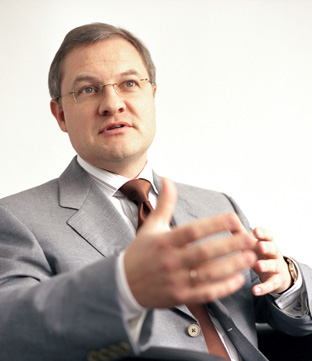
Swiss iQ Power AG develops and manufactures intelligent system solutions for electrical energy management in automobiles. Some of the company’s innovative products include the world’s first intelligent software-managed car battery – a quantum leap in battery technology. A new production plant is nearing completion in South Korea.
Peter E. Braun, the CEO of iQ Power, needs only a few words to sum up the dream of an entire industry: “To know at all times how much power is really left inside a batteryâ€.
So far, however, all attempts by the auto industry to come to grips with the complex issue of energy management with today’s lead/acid batteries have failed. The reason: Outdated battery technology and solutions that are too complicated.
Energy management can only work properly when the on-board computer reliably knows the battery’s states of charge and health (SOC/SOH). “A challenge that until now no one has been able to master satisfactorily,“ says Braun. The reason: The electrochemical process in lead/acid batteries is too complex to pack into an electronic battery model for managing energy.
One phenomenon in particular has proven to be a real conundrum: battery acid stratification. This problem is not merely a key cause for rising incidents of battery failure, it is also one of the major reasons why energy management has thus far performed so poorly. This is because acid stratification cannot be measured or reproduced in an electronic battery model. Not to mention the fact that stratification behaves differently in every battery and also each batter chamber and depends, among other things, on each vehicle’s own usage profile.
Stratification causes drop in battery performance of up to 40 percent within weeks
The speed and intensity at which this phenomenon appears are particularly great in batteries that have to power electrical systems with a large number of loads. This is the case in about 80 percent of all new vehicles. The consequences are quite severe. After only a short few weeks even brand-new batteries can show a massive drop in performance of up to 40 percent of their original rated capacity. This is because large portions of their lead surfaces are no longer active (dead lead). Throw in a weak back charge in cold weather, such as in winter, and it’s the end of the road for these batteries.
Even absorbent glass mat, or AGM, batteries really don’t help much. Here cellulose or fiberglass soaked with electrolyte slows the process of acid stratification. And yet this costly method helps only a little: Studies have shown that these twice-as-expensive rechargeable batteries far too quickly lose over 20 percent of their nominal capacity.
This is why European car makers such as Audi, BMW and DaimlerChrysler are demanding from batteries an improved charging capability in winter, along with active measures to permanently prevent acid stratification.
A quantum leap in battery technology and a tremendous increase in performance
“This is exactly what our technology has achieved. This technology of ours not only represents a quantum leap for today’s lead/acid batteries, but also a tremendous increase in performance,“ says iQ Power boss Peter E. Braun.
Instead of trying to pack all those trouble-causing influences and factors into a highly complex mathematical model, iQ Power (www.iqpower.com) engineered a more practical solution: Thermal insulation surrounding the battery ensures an even temperature and protects the battery against damaging spikes in temperature. An electronically managed foil heating maintains optimal electrolyte temperature, while specially formed plastic elements effectively prevent acid stratification in the battery cells. “You can only get a grip on the mathematical battery model once conditions have been made much simpler,“ explains Braun’s partner Dr. Günther Bauer, responsible for R&D at iQ Power. The clear benefit: The solution from iQ Power is technologically simple, costs less and is remarkably reliable thanks to the almost ideal environment within the battery. And because of the optimal stoichiometric relationships, iQ Power needs some 25 percent less lead in its batteries, which means six to eight kilograms less weight per battery. “This is a major contribution to support sustainability on the part of iQ Power,†emphasizes Bauer.
The vehicle’s own kinetic energy is one thing iQ Power uses to uniformly diffuse and mix the electrolyte in the battery cells and put an end to acid stratification. Plastic parts in each battery chamber form narrow vertical flow channels that direct the acid upwards from the base of the battery. “A simple hydrodynamic process,“ Bauer points out, “and a solution that is as economical as it is effective, and one that has an enormously favorable impact on the battery model’s reliability and delivers more performance from lead/acid batteries.â€
Batteries with iQ technology will first hit the market in 2007. A new factory capable of producing at least 3.5 million units is being built as part of a joint venture in South Korea. Other licensing partners are waiting to come on board. The publicly listed iQ Power company also has plans for Germany.
Benefits of iQ Power’s Ingenious Battery System
~ More reliable SOC/SOH/SOF status thanks to a precise battery model.
~ More ampere hours available, as no losses in capacity from acid stratification.
~ Greater cycle stability, since there is no loss of active lead in the battery.
~ Superior back charging capability, as the sulfate crystals remain at an ideal, microscopic size. Added electrolyte temperature controls optimize the charge factor in winter (critical for short-distance driving).
~ Your choice of reduced weight (25% less lead, ca. 7 kg lighter) or greater capacity.
~ Autarchic, self-enclosed system solution, making it perfect for after-market installation as well.
~ Data communications with the car’s on-board computer via energy store’s terminal clamp using built-in Powerline Communication (PLC).
~ Battery’s history is always known (product includes data logger), thereby ensuring that any abuse is clearly tracked and identified.
~ Extended service life through a generally more conservative battery operation.
~ Better overall performance compared to AGM batteries. Costs less than AGM.
Background: The Difficult Issue of Acid Stratification
Today’s wiring systems with their many electrical loads and consumers put a strain on car batteries like never before. Battery discharges of up to 50% of their rated power (SOC = 50%) can easily occur. These kinds of deep charging cycles accelerate destructive acid stratification and reduce cycle stability.
Fully charged batteries have an electrolyte with a high acid concentration, while deeply discharged batteries contain pretty much only water. When that happens, the entire sulfate has bonded with the lead in the battery’s plates. If the battery is now charged with current from the car’s generator, the sulfate in the plates then separates from the lead and forms an acid which, because of its greater density, sinks to the bottom of the battery. As a result, more sulfate collects in the lower part of the lead plates than near the top the next time the battery discharges. This has a reinforcing effect throughout each cycle as the acid builds up layer upon layer.
Such layering, or acid stratification, throws the stoichiometric ratio in the battery out of balance. Water prevails in the top third of the battery while most of the sulfuric acid is in the bottom third. The result: Active charging surfaces are lost and the nominal capacity of the battery sinks. After only a few short weeks the amount of loss could reach up to one-half the original power rating. The battery’s cycle stability also declines from having so little active lead remaining in the battery. Premature corrosion (concentrated acid) in the lower part of the lead plates leads not only to further losses in performance, but to a buildup of sludge until the battery dies. Icy temperatures in winter help weaken batteries even further
Automotive Industries spoke to Peter E. Braun, CEO of iQ Power AG, about the future of energy storage systems in automobiles.
AI: How do you see future energy storage systems for automobiles evolving?
Peter E. Braun: First let me point out that we will continue to see today’s lead/acid technology in starter batteries for a very long time, despite ideas to supplement them in cars with such things as lithium-ion batteries or supercaps. The advantages of lead/acid are still unmatched. And I believe that the potentials in performance and capability of today’s 12-volt lead/acid technology are far from being exhausted. With a systematic approach and new technologies like those we’ve developed at iQ Power, we can extend these limits a lot further.
AI: Could you be more specific? And what does this mean in terms of energy management?
Peter E. Braun: Our product – a smart car battery – clearly proves that recognized drawbacks, such as poor charging in winter or a loss of performance from acid stratification, can be effectively eliminated while at the same time greatly improving the cycle stability of wet batteries. Overall our system technology achieves significantly better ratings than for example AGM batteries, along with an average of twice the battery life. We use a new S curve to extend the life cycle of today’s lead/acid technology. The fact that our technology can accurately and reliably determine the battery’s state of charge (SOC) and state of function (SOF) means that we have for the first time laid the foundation for what is truly a functional energy management in the automobile, namely the communication between the smart energy store, the generator and the electrical loads.
AI: iQ Power is building a factory for smart batteries with its venture partner in South Korea. What made you pick that location?
Peter E. Braun: South Korea is an extremely attractive automobile market with a dynamically growing motor-vehicle industry. Auto makers in Korea, like in Asia as a whole, are extremely interested in innovations that make their cars more reliable and more responsive to the wishes of their customers. This is the backdrop as to why Korean manufacturers have such a great interest in our technology and products. In a joint venture with our Korean partner we’re now building a factory for smart batteries that will have an initial capacity of 3.5 million units. After all, these batteries also fit perfectly in existing vehicles and will provide benefits for OEMs and consumers alike.
AI: Can other battery makers be licensed to use iQ Power’s technology?
Peter E. Braun: Yes, our technology is available under license to any battery manufacturer. This is an excellent opportunity for licensees to set themselves apart from the competition with vastly more capable products and greater added value. One of the advantages of our technology is that the modifications to today’s products will be very minor, allowing them to be manufactured using the same plants and equipment.
AI: What kind of products are on the drawing board at iQ Power which you think will revolutionize the energy management systems of vehicles?
Peter E. Braun: iQ Power has sole responsibility for the issue of energy management as an engineering partner in SPARC, an EU project for drive-by-wire vehicles under the leadership of DaimlerChrysler. Such an undertaking demands totally new types of energy architectures, concepts and solutions. What’s more, we are also working on energy architectures of lead/acid batteries and supercaps for use in hybrid vehicles.
For more information please visit:
More Stories
Huntsman Polyurethanes introduces a new range of polyurethane-based products developed for battery enclosures, battery cell potting and underfloor protection
Lakshmi Prasad Bhatta on the quest for zero road deaths
NXP accelerates the development of software defined vehicles with new family of Ethernet switches