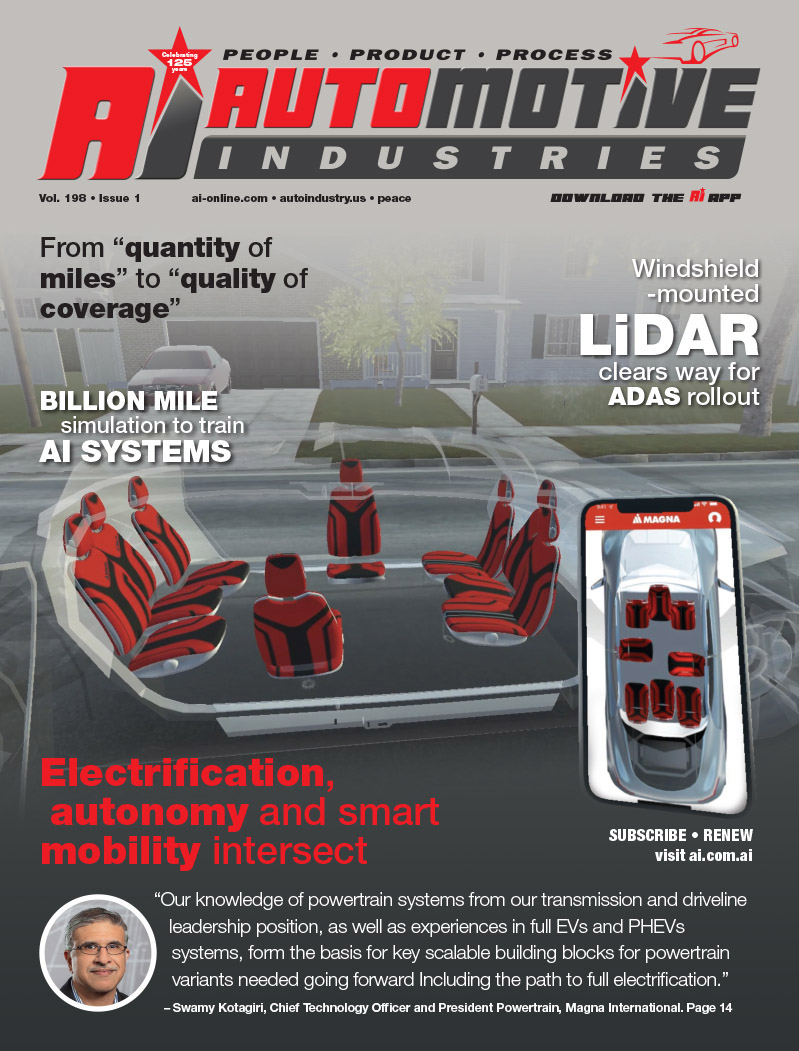
“Restraint systems must meet increasingly more complex legislation and requirements, whilst development cost and time has to be reduced”.- TASS chief executive officer John Cooper.
The Netherlands-based TASS (TNO Automotive Safety Solutions), recently launched a research project into real time restraint control.
Real time restraints sensors measure the severity of the crash and the loading on the occupant. This information is used to control the pulling by the seat-belt and the deployment of the airbag during the crash, TASS chief executive officer John Cooper told Automotive Industries.
Cooper says earlier legislation allowed engineers to develop a solution for one design point and this could be handled by the engineer. Today the designer has to meet the requirements of multiple design points and sometimes these design points do not complement each other (i.e. belted and unbelted occupants). In this case an optimization process has to be used and MADYMO provides that capability. In conjunction with its optimization partner ESTECO which developed ModeFrontier, MADYMO is capable of solving complex multi-point design points and producing a single design solution.
TASS software code applied to the safety of occupants and pedestrians in transport related safety conditions is known as the MADYMO. According to Cooper, MADYMO recently developed pre- and post- processing capability that enable both MADYMO experts and novice users to build models, execute simulations and analyze the results very efficiently and in a controlled manner. The future focus is to develop a solution based software package that provides optimal solutions to an increasingly more difficult set of design conditions. The user will define the problem and the MADYMO software will help them to develop a design specification that meets or exceeds the requirements.
“The new challenges are very simple. Restraint systems must meet increasingly more complex legislation and requirements, whilst development cost and time has to be reduced. The effect of both has a compound impact on all companies involved with virtual development,” says Cooper
Costs are also a factor, and a major objective of TASS is to reduce the cost of development by 50% every five years, he says.
TASS is negotiating with several OEMs to study requirements for real time restraint control. TASS is also in close cooperation with Denton ATD, a leading manufacturer of crash test dummies, as well as the Partnership for Dummy Technology and Biomechanics (PDB) alliance. This includes Audi, BMW, DaimlerChrysler, Porsche and Volkswagen.
Automotive Industries asked Cooper for an update on the company’s work with real time restraint controls.
AI: Will real time restraint control be a requirement under law in the future?
Cooper: This is highly unlikely. Typically, legislation identifies some type of measured result that leads to a legislation metric, Head Injury Criteria (HIC) for example. This allows the industry to define their own approach to meeting the requirements. What is clear is that as legislators continue to refine the requirements it is less likely that the industry will be able to meet those requirements using passive safety.
AI: What are some of the other technologies that TASS is working on for in-vehicle safety?
Cooper: The role of TASS is to provide software solutions and engineering methods allowing OEM’s and suppliers to meet research, design and development requirements. Therefore, TASS is working on a range of software tools and methods to compliment the future requirements. The physical safety products are developed by the OEM’s and suppliers.
More Stories
Shaping the future of the automotive industry at Automechanika Shanghai 2024 with the most fringe programme events and speakers yet
Some Ways How Motorists End Up in Collisions at U-Turns
Maximise Margins with Proven PPF Tactics