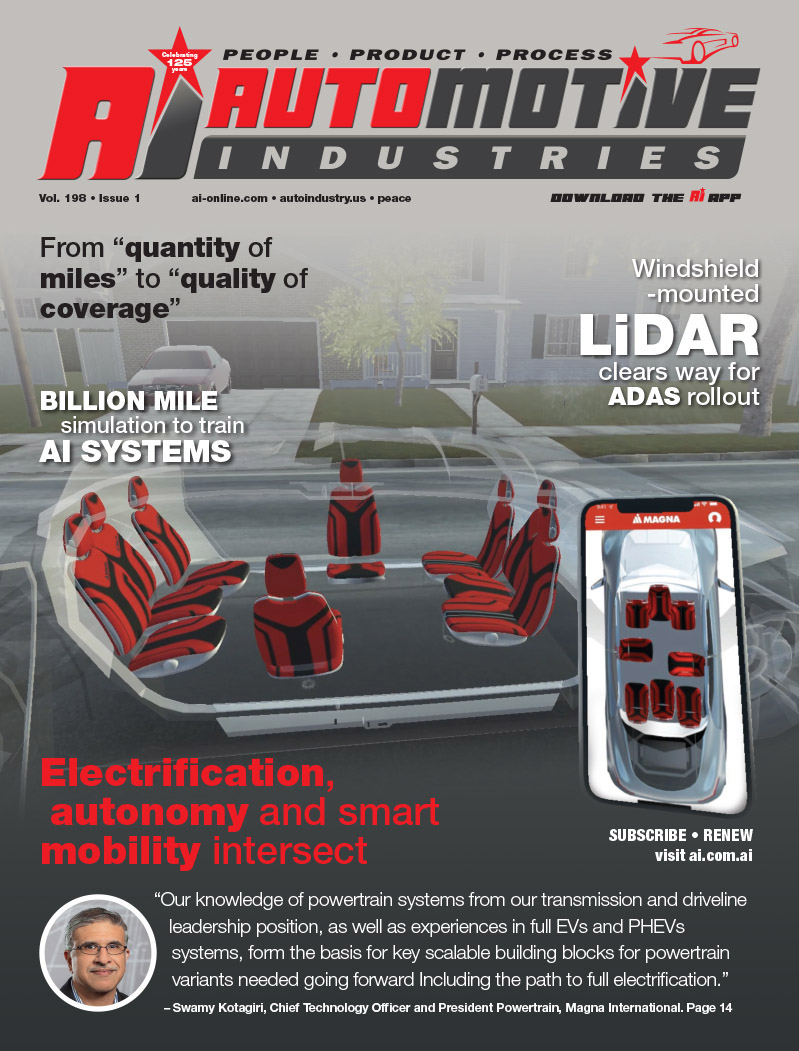
Automotive Industries talks to Thomas Kraus, automotive sales director at Rasmussen.
Automotive Industries (AI): You are one of the leaders in the field of connecting and retaining technology. Please introduce the product range to our readers.
Kraus: Rasmussen GmbH and its world-wide 10 subsidiaries in Germany, UK, France, Spain, Italy, USA, Poland, Australia, China and Singapore also known as NORMA Group is a global, first tier supplier of production stage components and systems to the automotive industry. Under the trademark NORMA, we are a world leader in the design and manufacture of quick connectors, media transportation lines and customised solutions for fluid and air applications. Our range of connecting and clamping products is the most comprehensive available and is unsurpassed in both performance and quality. Be it hose clips or exhaust pipe clamps, Rasmussen can provide the optimal solution for every application. Extensive production capabilities, coupled with lightweight and space-saving designs, mean that our products can significantly reduce assembly times and are a highly cost effective choice.
AI: How do you see the future for interfaces in exhaust systems – clamps versus flanges?
Kraus: Until today it was a common technology to use two or three bolt flanges for connecting exhaust systems to manifolds or turbo chargers respectively and connecting the interfaces in exhaust or EGR systems. But new legal requirements and new OEM programs for weight and cost reduction demand for new connecting technology.
AI: Can you tell us about your new developments in the areas exhaust systems?
Kraus: In our business area NORMAFASTEN we developed two new kinds of modular systems of clamps with special flanges that can be used as innovative, alternative connecting technology in modern exhaust systems.
First is our NORMACONNECT SEC (swivel joint exhaust pipe clamp) which is developed for the rare and centre section of the exhaust system. It can be used up to a surface temperature of 580 °C. The leakage rate is less than 2 liters per minute and if you use a gasket it is less than 0,1 liters per minute. The dimensions are smaller than a two bolt flange and the possibility of angle compensation avoids tensions in the assembled exhaust system. The bending and torsion torque is minimum 150 Nm.
The second area is the development of our NORMACONNECT V QRC and V PP clamps. They are two new kind of profile clamps with a quick release closure and a pressed profile version. These clamps can be used on a special flanges with or without a gasket in the front section of an exhaust system. They were designed to connect the interfaces before and after the turbo charger or to connect the exhaust system to the manifold. They also were tested to be used as connection technology for diesel particle filters. The clamps and interfaces are released to a maximum gas temperature of 1200°C.
AI: What are the benefits of your new developments for the exhaust system and which carmakers have already implemented the new products?
Kraus: The benefits of these two new kinds of interface solutions are less weight and smaller dimensions than existing connection technologies. The leakage rates meets the new legal requirements and cost savings are higher than 25% as compared to other solutions. Because of the modular systems there are no additional tooling costs required.
The SEC clamp was at first introduced by DaimlerChrysler in the new M-Class and is now released for all platforms. For the C-, E- and S-Class it is already in series production for all diesel engines. For two years, BMW has also been using the SEC clamp for the exhaust systems for motorbikes. In addition it has been released for a new SUV which will be produced beginning September 2006.
The QRC clamp is used by Volkswagen for various applications.
The annual quantity for 2006 is 1.5 million clamps. For 2008 the introduction of additional applications like the fixing of exhaust flaps and diesel particle filters is also being planned.
Since the beginning of 2005, BMW has been using the NORMA® profile clamps at the interface before and after the turbo charger at all 6 cylinder diesel engines. We plan to introduce the all-new turbo charged petrol engines in the middle of 2006.
AI: What is the potential for using new materials in the field of fluid systems?
Kraus: In our business area NORMAFLUID we are equipped with the same research and development force as in the business area NORMAFASTEN. Here we developed, designed and tested some new pipe systems for hydraulic clutches, transmission oil cooling and cooling water applications. We replace the traditional assemblies out of metal pipes and elastomer hoses by light-weight but strong plastic tubes which are equipped with our NORMA Quick Connectors instead of clamp connections. To meet the specific requirements we use new materials that are developed in our research centre and released in our accredited test laboratory, where we can simulate almost any real-life situation of a car.
Because we offer complete systems with perfectly matching components the benefits for the OEM’s are reductions in weight up to 70% and cost reductions that amount up to 40% as compared to the former part price.
AI: What is your approach when it comes to the development of new customer-specific product? Do you use pre-developed concepts?
Kraus: The NORMA Group is not organized like a me-too-supplier. We understand ourselves and operate as a partner who supports his customers from the beginning of an idea until series production. We develop, design and test new, innovative concepts and products which are at first released on our internal specifications. We present these pre-developed innovations to our partners and modify them until they fit into the OEM’s concepts and specifications. With our local teams of engineers, resident engineers, sales and quality force we are able to react very flexibly to the customers’ demands. This procedure saves time, resources and money on both sides.
AI: What are the biggest challenges you face in meeting the OEM’s requirements for zero-defect target and at the same time delivering state-of-the-art volume production?
Kraus: Today’s state-of-the-art volume production needs a high rate of flexibility. As you can imagine NORMA Group has a product range of 20 000 different items and produces 3.5 million hose and pipe connectors per day. On the other hand, it is absolutely necessary that our production sides are equipped with a high grade of fully automated machines. This is the basis for the high quality level that is necessary to meet the zero-defect target. But the investment for these fully automated production machines is so tremendous that it can only be feasible with maximum high volume products. For mid and low volume products we use semi-automatic production and assembly machines. For that we need a highly skilled operating staff and additional quality checking systems. To minimise these additional costs we transferred the production of mid and low volume parts to our plants in low cost countries.
More Stories
LED Lighting for Heavy-Duty Applications: Durability, Efficiency, and Versatility
Celanese Materials Shine in Multiple Category Winners at 2024 SPE Automotive Innovation Awards
New future-ready single-slot PXIe controller for high-performance T&M applications from Pickering Interfaces