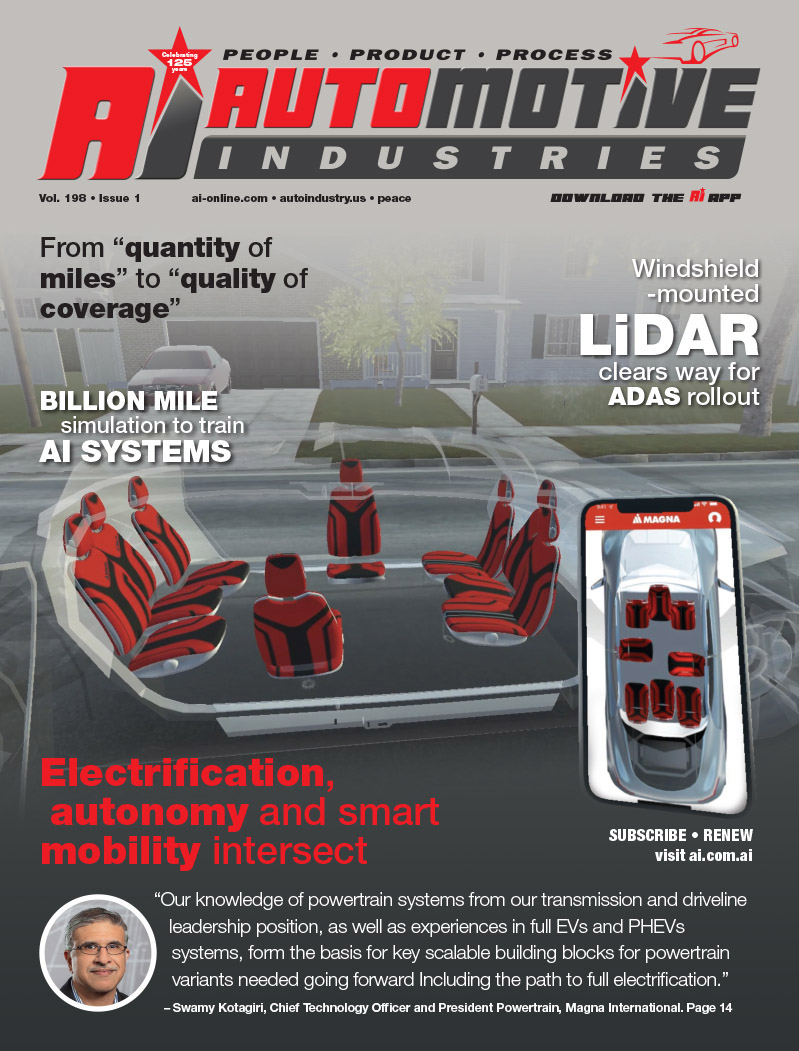
Increasingly tough emission legislation has created demand for a new generation of exhaust and air compressor seals. Nick Palmen of Automotive Industries spoke to Tim Fralick, director of sales and marketing at OILES America and Matthias Zeischke who is the sales manager of OILES Germany – one of the world leaders in this technology.
Automotive Industries (AI): Your products can be found in exhaust, steering, suspension and hinge systems. How does that balance your portfolio?
Fralick and Zeischke: Yes, the areas mentioned are our main focus areas for the automotive industry. As for exhaust applications, we are supplying approximately 20 million seal bearings per year for the decoupling of engine rolling motion and vibration to the exhaust systems in Asia, Europe, and North America. OILES is a dominant global supplier of rack bushings and support yokes, providing guiding support to the rack bar in the steering gear box. We have had significant success in the integration of plastic sliding bearings for the suspension strut mounts, displacing traditional needle and roller bearings. OILES also has a diverse line of plastic and steel backed multilayer bushings for door hinges, pedals assemblies, etc.
We have developed many products for other automotive applications. Some examples are: seat dampers for reclining seats; sliding bushings for A/C compressors; timing and accessory belt tensioners; shock absorbers and strut rod guides; convertible tops, retractable hardtops, and sliding doors.
AI: In which segment do you see the biggest potential for growth?
Fralick and Zeischke: In Japan, OILES has had significant success with the application of our exhaust seal (OILES #550) by Toyota, Honda, Nissan, Suzuki, and others. We are presently in nearly every passenger vehicle. This technology utilises a spring loaded spherical joint instead of a traditional flexible tube. We see a significant potential for growth in this area because of cost, packaging, and performance benefits. This technology is nothing new to the auto industry, and in fact can be traced back more than 25 years. However while the United States and European markets were struggling to integrate this product and overcome noise and leak concerns, OILES was perfecting the technology through the development and application of proprietary materials. Significant breakthroughs were achieved in the reduction of noise as well as the suitability for higher temperatures and improvement in overall durability.
It should be no secret, as evidenced by our long relationships and success with the Japanese OEM’s, that the OILES #550 technology continues to provide exhaust decoupling benefits. In addition to exhaust products, we expect rapid growth for CO2 (A/C) compressor applications. With an increasing rate of vehicles being standard equipped with air conditioning, the performance and cost advantages of our OILES Drymet product can’t be overlooked.
AI: Are you focusing on different areas of the automobile in different parts of the world?
Fralick and Zeischke: OILES has made a commitment to be a “Global” supplier of self-lubricating bushings and has established strategic manufacturing in Asia, Europe and North America. We continue to offer our full compliment of bushing solutions to all customers in all regions. We have established a solid network to share relevant information between global subsidiaries to leverage our vast application experiences, and desire involvement with our customers during the earliest stages of concept development. We have the capability of managing technical projects from one location while mass production takes place on another continent. We believe it is extremely important today to provide our customers with a strong global network and technical support.
AI: Your seal bearings for the exhaust system can be found in nearly 100% of the Japanese cars. How do you target new customers?
Fralick and Zeischke: We are promoting both to the OEM’s and Tier 1 exhaust integrators, depending on who decides how to decouple the exhaust system. So our customer base is expanding globally as we introduce our technology to other Automotive OEM’s and their designated integrators. In addition, the range of applications has increased for the OILES #550 gasket as larger displacement vehicles are trying to achieve lower NVH and increased durability. OILES is focused in understanding and modelling the full exhaust to be able to recommend optimum positioning of our products for maximum performance.
AI: Is there a difference in your approach in Europe, US and the rest of the world?
Fralick and Zeischke: No – OILES is committed to being a global supplier and standardising our approach to support our global customers. There are similar challenges in many of our key markets, regardless of location.
AI: What are the main advantages of OILES bearings in terms of cost and weight reduction?
Fralick and Zeischke: Depending on the product, OILES strives to be the value leader in our products. This does not necessarily mean the lowest cost, but when performance and technology are considered – OILES products are world class. The high performance of our materials makes it possible for OILES to be successful in applications where our competitors can’t. This translates many times into significant savings, especially when the designer is able to achieve adequate life using a plain bushing versus a rolling element bearing.
AI: How early do you get involved in a project? Do you work with the carmakers from early developing stages or do you come aboard later?
Fralick and Zeischke: Of course we typically would prefer to be involved with our customers from the earliest stages of concept development thereby allowing for the optimum bushing recommendation or in some cases the development of a custom product. We have made significant strides in CAD/CAE and predictive modelling, so we can provide value to our customers during this early design stage. However, the nature of some of our products and customers demand that we get involved late in development and often find ourselves in a position needing to provide a quick solution to a problem during design verification stage. OILES has an advantage here in that we have a significant application experience and a wide offering of materials. We are often very comfortable and successful in this position.
More Stories
LED Lighting for Heavy-Duty Applications: Durability, Efficiency, and Versatility
Celanese Materials Shine in Multiple Category Winners at 2024 SPE Automotive Innovation Awards
New future-ready single-slot PXIe controller for high-performance T&M applications from Pickering Interfaces