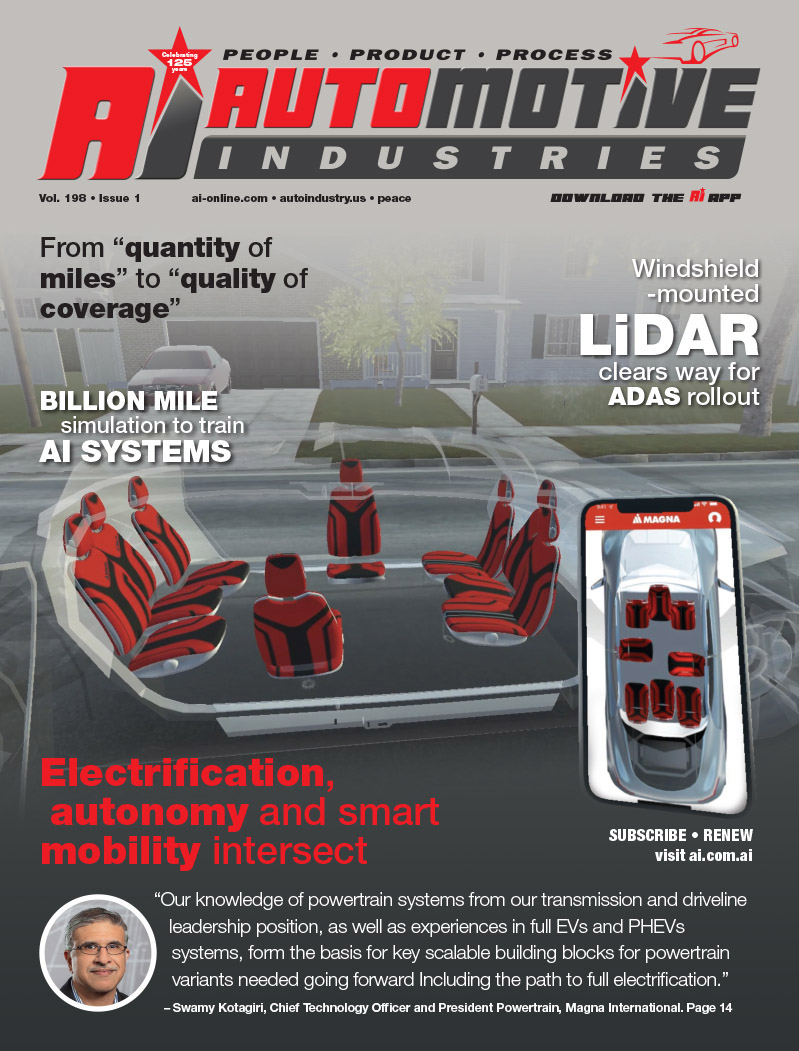
Michigan-based Spiralock Corporations proprietary, self-locking internal thread form has been providing OEMs with reliable fastening solutions for many years and continues to expand its applications in a wide range of industries, including automotive, aerospace, defense, medical implants, farm equipment, oil exploration equipment and others.
Spiralock internal thread form was designed to address the fastener loosening and stripping problem caused by vehicular vibration, shock, and temperature extremes. The secret to Spiralocks thread form is a 30 degree – wedge – ramp cut at the root of the female thread. The wedge ramp allows the male fastener to spin freely relative to the female thread and eliminate galling. When clamp load is applied, the crests of the standard male thread form are drawn tightly against the wedge ramp, eliminating radial clearances and therefore, any transverse motion that causes loosening under vibration.
Once clamp load is applied, it establishes a continuous spiral line of contact along the entire length of thread engagement, which more evenly distributes the loads of the threaded joint throughout all the engaged threads. Research studies performed by Lawrence Livermore National Laboratory, Massachusetts Institute of Technology and others confirms that the percentage of the load carried by each Spiralock thread is much more uniform than with conventional 60degree thread forms, giving the thread better fatigue performance. Additionally, they show that the percentage of load on the first Spiralock thread is significantly lower (24% versus 64% with five engaged threads).
Additionally, contact forces between the male crest and female wedge ramp are applied at approximately 60 degree from the bolt axis as opposed to 30 degree with the standard thread form. This mechanical advantage – the angular relationship between the unique wedge ramp and the male thread – takes advantage of the hoop strength of the material for improved joint integrity.
Spiralock threaded holes and nuts accept standard male fasteners and eliminate the need for secondary locking devices such as lock washers, adhesives, patch bolts or crimping, thus simplifying assembly and reducing costs and warranty problems.
Faced with challenges of extreme weather and terrain conditions, shock, vibration and thermal stress, the automotive industry utilizes Spiralock thread form in many applications, including axle housings, brake bearing hubs, brake calipers, bumper attachments, chassis assemblies, differential guards, exhaust duct supports, exhaust heat shields and skid plate mountings, exhaust manifold joints, hydraulic pump attachments, intercooler control valves, output pinion shafts, power steering pumps, ring gears, running board attachments, shock absorber mounts, split differential housings, torque converters, trailer hitches, transmission housings, turbine housings, turbocharger attachments, housings and support brackets.
Among companies served by Spiralock Corporation and its subsidiaries in Europe, Asia and South America are General Motors, AM General, Ford, Daimler Chrysler, Toyota, Land Rover, Volvo, Mitsubishi, Nissan, Borg Warner, Dana, Delphi, Honeywell, International, Allison Transmission and others.
Automotive Industries asked James P. Gillis, Executive Vice President and Chief Operating Officer at Spiralock Corporation about the companys latest technology breakthroughs.
AI: What are some of the new products we can expect to see from Spiralock over the next year?
Spiralocks mission as a leading international fastening solutions company is to develop innovative products to help our customers solve problematic fastened joint applications. Our Application Engineers work with our customers to identify challenging applications while in the field, which translate into wonderful opportunities for our R&D Staff in Michigan. We are able to develop many new products annually that meet our customers application requirements.
This year, the Company is in the process of launching a new V-band Clamp Nut for use in high temperature exhaust applications. The nut is designed to eliminate galling inherent in these applications due to the long run down on the male thread, in addition to providing unlimited reuse while maintaining its locking feature. The nut also has extra thread length and load distribution for improved fatigue performance.
We are also developing our manufacturing capability for thin walled nuts, which provide weight savings as well as better balancing associated with the self centering aspect of Spiralock threads and closely held perpendicularity of the nuts. These nuts are used in turbo charger applications as well as auto racing and aerospace applications where weight reduction is important.
Additionally, Spiralock has a new style of wire thread insert that eliminates the installation tang. Normally, the tang must be removed and captured during assembly in many applications, which is difficult and costly during manufacturing. The new wire thread insert is called the Spiralock Drive Notch TM Insert and should be available later this year. Spiralock wire thread inserts are utilized by diesel and gas engine manufacturers as well as aerospace companies. Wire thread inserts are utilized in soft materials such as aluminum or magnesium to provide the threaded joint with added strength, secure locking and multiple reusability.
Furthermore, we have many projects under development to solve specific threaded joint applications, including: a nut that will free spin onto a bolt and have prevailing torque to prevent it from coming off, a locking fastener for soft joints (i.e., gasket), a tamper proof nut with special exterior geometry, and others.
AI: What percentage of your revenues comes from the automotive sector and by how much do you see this sector growing?
Five years ago, Spiralock Management made a decision to focus our resources in specific industries where we could have the greatest influence and impact. We established six primary industries in which to focus our technical people: aerospace/defense, automotive, heavy truck, medical (mainly orthopedic implants), farm/construction equipment and oil & gas/power generation.
The results have been very positive for the Company, which has experienced an average annual growth of 24% over the past four years. The automotive sector represents 20% of our overall business. We anticipate this sector to have the largest percentage growth over the next five years, partly due to our efforts in Asia, Europe and South America.
AI: In which geographical areas of the globe has Spiralock grown fastest?
We have experienced substantial growth in our Company over the past four years, averaging 24% globally. All of our business units have achieved double digit growth during the period. Our most recent expansions into Brazil and China have resulted in significant business in a short period of time, averaging growth of 90%+ each of the past four years. Our more established business units (US and Western Europe) have experienced growth in the 15-30% range over that same period.
We anticipate another increase of 23-27% in global revenues in 2006 with Europe seeing the highest overall growth in the range of 40-45%.
AI: What are your plans for further expansion both at home and globally? Any new manufacturing plants? If so, where?
We are continually looking at the needs of our customer base to plan our expansion. I can tell you that it is typically the automotive industry that drives our expansion because the automotive sector is the leader when it comes to developing manufacturing capability and engineering expertise on an international basis.
Presently, we are planning on opening a new operation in mainland Europe shortly after the first of the year to better support our customer base in Western and Eastern Europe.
We are also investigating the possibility of opening operations in Japan, Thailand and India similar to our European operation to support our customers in those areas.
More information on Spiralock can be found at http://www.spiralock.com/
More Stories
AUO Returning to CES Showcase Next Generation Smart Cockpit 2025
Donaldson Ultra-Web technology aims to set the standard in industrial filtration for cleaner air and cost-savings
Hydrogen’s Role in Decarbonising Sports and Entertainment Events