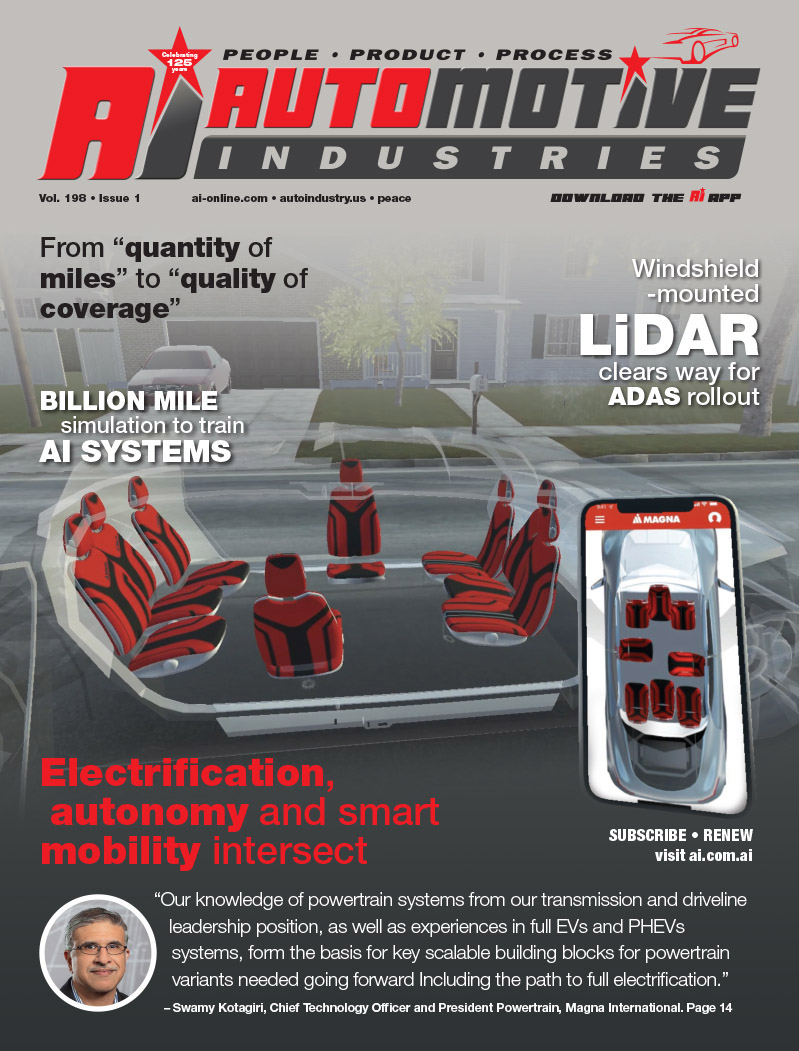
Converting Film Into Fashion
Laminates can provide more trim options yet keep costs in check.
![]() |
Avery Dennison brings the PT Cruiser’s exterior color to the interior. |
“Fashion sells. It’s becoming normal for us to supply four or even five finishes for the same model, regardless of whether it’s a car, truck or SUV” Michael Kozbial, senior marketing manager, Avery Dennison’s Performance Films Division, tells us. “On Ford’s new F150 center console, for example, we supply Thermark laminates in Pewter Wave, Brazilian Oak, Dark Mandarin Teak, and Harley Davidson Barn Shield.
“The offerings are becoming more diversified among the metallic, geometric, woodgrain and organic patterns. Pearlescent finishes are more popular. There is also a trend of bringing exterior colors back into the vehicle such as on the PT Cruiser and Mini Cooper. Laminates are an effective way to accomplish that as well.
“And, of course, the quality also keeps evolving to higher levels with greater DOI (Distinctness Of Image), higher gloss. harder, more durable and fade resistant finishes.”
Another high profile model for the application of Thermark is the new Toyota Solara, where Avery Dennison has designed and produced two new patterns: Magma Birds Eye woodgrain and Sport Fiber geometric laminate.
For nearly 30 years Thermark laminates have been applied to countless interior parts such as instrument panels, center stacks, consoles, air bag covers, switch plates, door and seat accents.
These laminates are produced by reverse gravure printing the pattern to a durable clear topcoat and laminating that film to a backing sheet of various resins like ABS, TPO and polycarbonate. The film laminate is supplied in roll form.
Film is converted into preformed shells by vacuum thermoforming. Shells are then trimmed to the desired shape by die, laser or water jet. The trimmed preform is then placed in a mold cavity of an injection molding machine where it is molded to the same material used in the backing sheet.
If some texturing is desired, different affects can be achieved by applying texture to the cavity of the mold itself. Further in mold decoration is also possible. Pressure sensitive graphics can be applied directly to the preform prior to molding. The graphic is forced into the film surface during the molding process giving it a “zero profile” look.
With laminates, parts can be changed with no tooling expense achieving a new look for the part, the ultimate in flexibility.
More Stories
Easy Car Maintenance Tips to Prevent Accidents Due to Malfunctioning Parts
Exploring the Best 2024 Jeep Gladiator Add-ons for Performance and Style
Maximizing Tire Life with the Right Air Pump for Car Tires