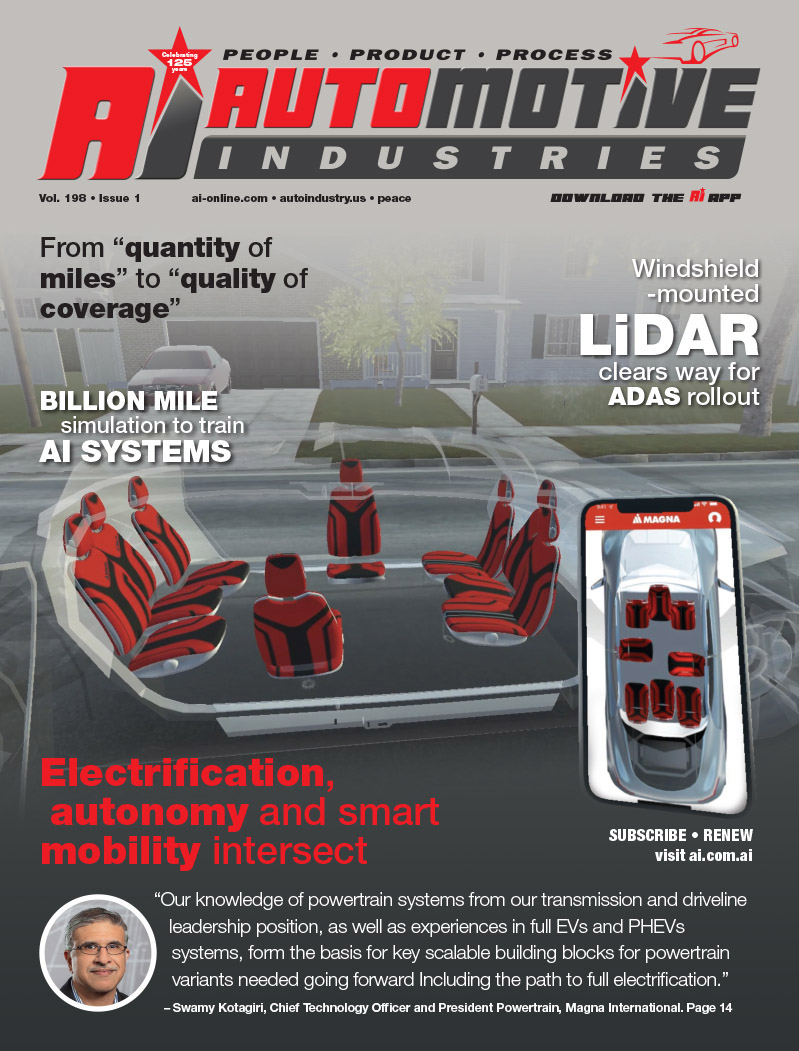
KS Aluminium-Technologie AG is the master at making ALUSIL low-pressure diecast engine blocks.
In the late 1970s, ALUSIL engine blocks made by low pressure die casting (LPDC) had found a place in SI engines for passenger cars in Germany. Aluminum was chosen as a substitute for grey castings to achieve weight reduction. A Porsche Cayenne engine block passes through one of several cleaning stations on its journey through finish-machining.
Since then KS Aluminium-Technologie AG, a division of Kolbenschmidt-Pierburg, has been a supplier of aluminum engine blocks in V arrangement, namely those made from the hypereutectic aluminum-silicon alloy ALUSIL.
The following are current engine block customers with KS Aluminium-Technologie AG: 4.0L V-8 (Jaguar), 4.0L V-8 Supercharged (Jaguar), 3.6L V-8 (BMW 735i), 4.4L V-8 (BMW 745i), 6.0L V-12 (BMW 760i), 6.0L W-12 (VW & Audi), 4.0L W-8 (VW), 2.5L R5 TDI (VW), 5.0L V-10 TDI Biturbo (VW Phaeton/Touareg), 4.5L V- 8 ( Porsche Cayenne), 4.5L V-8 Turbo (Porsche Cayenne), 3.4L Boxer 6-cyl. (Porsche 911 Cabriolet & 911 Carrera Coupe), 1.4L inline 4 (A-Class), 1.6L inline-4, (AClass), 1.9L inline 4 (A-Class) 1.6L Diesel (AClass), 1.9L Diesel (A-Class).
They also supply for the Volvo S60 and S80 as well as the BWM 5-series. Applying this technology to the VW “W” series engines was particularly challenging.
![]() |
The KS Aluminum Technology division has taken over the complete finishmachining process for the Porsche Cayenne engine block, a first for the company. |
ALUSIL technology produces monolithic aluminum blocks without requiring the additional reinforcement of the cylinder bores. The tribological properties can be attributed to the hypereutectic alloy AlSi17Cu4Mg and the precipitation of primary silicon which protects the cylinder bore surfaces by means of wearresistant grains. The VW W8 and VW/AUDI W12 engines represent the latest evolution of the ALUSIL concept.
To implement the fundamental design of the compact W engine concept in an appropriate method, a total of six sand cores were used. In the V section, this led to a primarily vertical layering of cores due to the two through-type horizontal decks. The LPDC method had to be adjusted to make use of its qualitative assets – the quasilaminar mold filling and directional solidification.
The directional solidification aspect can react extremely sensitively to the constraints in active cooling prevailing in the central area of the component. However, it is the contention of the company that the engine blocks of VW/AUDI with W arrangement of the cylinders prove that ultimately a compromise exists between high functional integration, cost-effective production and casting quality.
![]() |
Here is a newly-finished Porsche Cayenne engine block. |
The inserts consist of two double bosses with a bow-shaped connector. To the sides of the bosses and between them, underneath the bow, undercut and open-worked anchors are arranged to provide for positive coupling with the adjoining aluminum. The inserts are cut free in large areas to allow for the free wheeling of the crankshaft as the main bearings are narrow. That is why a solid anchoring system is needed.
The oil separator wall is integrated with the bed plates of the engines with wet-sump lubrication. The wall will route the oil selectively to the oil sump, simultaneously separating it from the crankcase to minimize oil foaming. This design is meant to provide additional rigidity for both the lower part of the engine block, bulkheads and side walls, as well as the overall component.
A challenge for W engine blocks was in areas where the bottom of the cylinders meets the bulkheads. There is an intersection of adjoining cylinders in that area where the crankshaft freewheeling would collide with the outlet for the honing tool. A central link of the bulkheads with the cylinder area calls for a short outlet (cut free area) for the honing tool and requires special machining techniques for the finishing work.
The cylinder wall tapering down to the point of intersection is straightened out by means of two longitudinal bores. The main oil duct is located in the top part of the oil pan. The bed plate with its plane surface seals on its bottom side (the interface between bed plate and oil-pan top).
From the main oil duct, the main bearings are directly supplied with lubricating oil. A riser leads to a central oil gallery in the V above the bulkheads. The gallery is pre-cast on both sides using steel cores and subsequently pierced through by drilling and closed from the outside with threaded plugs.
The other lubricating points and the splashoil cooling system for the pistons are supplied with oil from the central oil gallery. The unpressurized oil drain ducts from the cylinder heads are arranged on the outer sides, as in the case of V engines.
They differ in details of their arrangement (left and right sided, W8 and W12 blocks). The ducts are not pre-cast but drilled in inclined direction during pre-machining, or, in the case of collector ducts, also in longitudinal direction in relation to the engine. The oil drain ducts continue in the bed plate through to below the oil separator wall.
Cylinders in the W configuration include the large V angle formed by the two cylinder banks of 72 degrees. The cylinders of one cylinder bank additionally constitute a smaller V angle of 15 degrees, already the case for the VR engines of VW. The unusual compactness of the W engine results essentially from combining two 15 degree V’s into a single 72 degree V-shaped engine.
More Stories
Why Electric Mountain Bikes Are Changing the Game for Off-Road Cyclists
Understanding Your Rights After a Crash with a Motorcycle Accident Injury Lawyer
Bangkok International Motor Show 2025 – The Talk of Sensuous Automotive